When it comes to producing custom apparel, different printing methods can significantly impact the look and feel of your designs.
Direct-to-garment (DTG) printing is one of the most advanced technologies in the industry. Unlike traditional printing methods, DTG allows for high-resolution printing directly onto fabrics, effortlessly turning intricate and colorful designs into reality.
As a clothing manufacturer with years of experience, we deeply understand how each printing method affects the final product’s appearance.
We hope this article helps you better understand DTG printing technology and make informed decisions when choosing a printing method.
What is DTG Printing?
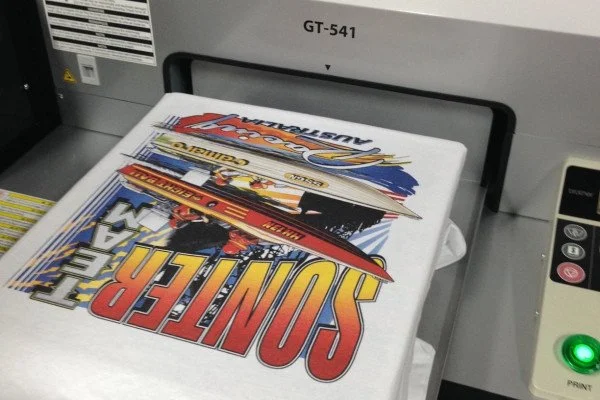
DTG printing is a method that uses specialized inkjet technology to print designs directly onto fabric.
Think of it as using a home inkjet printer, but instead of printing on paper, the “canvas” is a T-shirt, hoodie, or other garment.
This technology sprays ink onto the garment, where it is absorbed by the fibers, creating vibrant, high-resolution images that can capture even the most intricate designs.
Unlike screen printing, which uses stencils and layers of ink, DTG offers greater flexibility and a simpler process.
The Evolution of DTG Printing
The first DTG press was developed by Matthew Rhome, who patented the technology in 2000 under the name ‘Revolution’. DTG was initially a niche option due to limitations in ink technology and machine speed.
With The introduction of pretreatment solutions further boosted the technology’s popularity, enabling better ink adhesion and durability, especially on dark fabrics.
It wasn’t until the 2010s that DTG gained widespread acceptance in the custom apparel industry due to the rise of e-commerce and on-demand printing services.
How DTG Printing Works?
The DTG printing process is relatively straightforward but highly efficient, especially for producing small orders with detailed artwork.
- Design Preparation: The design is created digitally, usually using design software like Adobe Illustrator or Photoshop. It’s essential to ensure the artwork is high-resolution for the best print quality.
- Garment Preparation: Before printing, the garment is pre-treated with a solution that helps the ink adhere better to the fabric. This step is crucial for ensuring the print’s longevity and preventing the ink from washing out too quickly.
- Printing: The garment is loaded into the DTG printer, and ink is applied directly to the fabric in layers, similar to how an inkjet printer works on paper. This process allows for complex, multi-colored designs without the need for screens or stencils.
- Curing the Print: After printing, the design must be cured to set the ink. This is done using either a heat press or a conveyor dryer. The curing process ensures that the design is permanently bonded to the fabric, making it durable and washable.
- Final Inspection: Once cured, the garment is inspected for quality assurance. The final product is soft to the touch, as the ink is absorbed into the fibers, unlike screen printing where the ink sits on top of the fabric.
DTG Printing: Pros and Cons
DTG printing offers a variety of unique advantages over other methods, making it a popular choice for custom garment production.
But it’s not perfect, and you also need to be aware of its flaws to make a better choice.
The Pros of DTG Printing
High-Quality Prints with Intricate Detail
One of the biggest advantages of DTG printing is its ability to produce exceptionally detailed, high-resolution prints.
This process allows for gradients, shadows, and fine lines that are difficult to achieve with screen printing. It’s particularly suited for printing realistic images or designs with a lot of colors and complex details.
No Minimum Order Requirements
Unlike screen printing, which often requires high setup costs, DTG printing does not need screens or extensive preparation.
This means you can print a single shirt or small batches without incurring high costs. However, for large production runs, screen printing may still offer lower unit costs.
Fast Turnaround Time
Once the digital design is prepared, it can be printed almost immediately, allowing for a quick turnaround. This is especially beneficial for businesses needing to complete small orders quickly or those offering on-demand printing services.
Environmentally Friendly
Many DTG printers use eco-friendly, water-based inks that are safer for the environment. Additionally, since the process does not involve creating screens or using chemicals to clean screens, it generates less waste compared to screen printing.
As environmental concerns continue to rise, DTG provides a more sustainable option for custom printing.
Disadvantages of DTG Printing
Higher Cost for Large Orders
DTG printing is cost-effective for small runs, but for larger orders, screen printing may be cheaper due to economies of scale.
Limited Fabric Compatibility
DTG works best on 100% cotton or cotton blends. It can be less effective on polyester or dark fabrics without special treatments.
Slower Production Speed
DTG prints one garment at a time, which can be slower compared to methods like screen printing that handle bulk production more efficiently.
DTG vs Other Printing Methods
While DTG printing offers many advantages, it’s important to compare it with other printing technologies like screen printing and heat transfer printing.
DTG vs Screen Printing
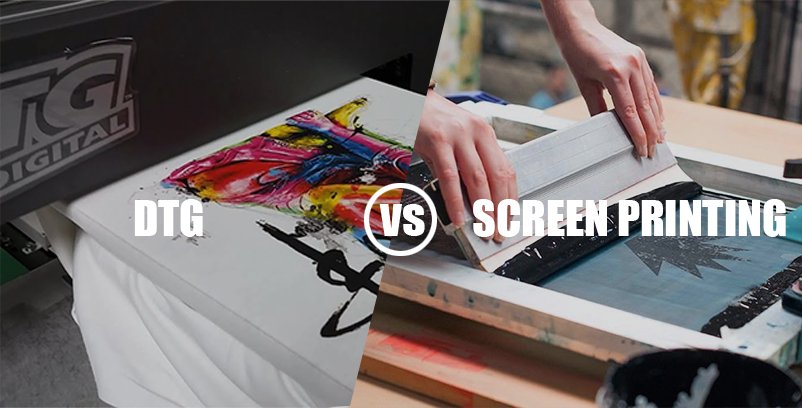
Screen printing is one of the most common methods for apparel printing and is durable and cost-effective for large orders.
However, it requires creating a separate screen for each color in the design, which increases setup time and costs. This makes it less practical for small orders or multi-color designs.
Screen printing often results in longer-lasting prints and can achieve more vibrant colors on dark fabrics.
In contrast, DTG excels at producing high-detail, multi-color designs, especially on light-colored fabrics. DTG is also better suited for on-demand printing and one-off designs.
DTG vs Heat Transfer Printing
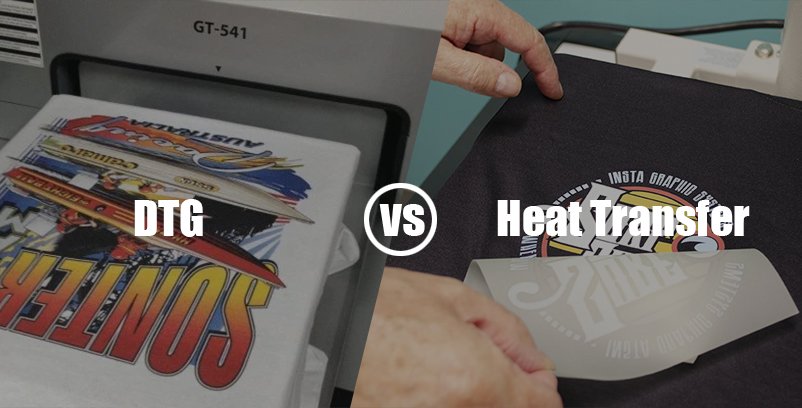
Heat transfer printing involves printing the design onto transfer paper and then applying it to the garment using heat. This method is often more affordable for small runs.
However, heat transfer prints generally sit on top of the fabric, giving them a different texture and potentially causing them to crack over time. DTG ink, on the other hand, is absorbed into the fibers, making it more durable and long-lasting.
Best Fabrics for DTG Printing
While DTG printing works on various fabric types, it performs best on natural fibers, especially cotton.
100% Cotton
Cotton is the best fabric for DTG printing because it absorbs the ink well, resulting in vibrant, detailed prints.
Natural fibers allow the ink to bond more effectively, producing a soft, durable print that feels like part of the garment rather than sitting on top.
Cotton-Polyester Blends
Cotton-polyester blends also work for DTG, though the results may not be as vivid as on 100% cotton. The polyester fibers in the blend may not absorb the ink as well, potentially leading to slightly faded appearances.
However, if you’re looking for garments with polyester durability and stretch, cotton blends are still a good option.
Organic and Sustainable Fabrics
As sustainability becomes a priority for many brands, organic cotton, and other eco-friendly fabrics are gaining popularity. These fabrics work well with DTG, offering high-quality prints and additional environmental benefits.
Common Questions About DTG Printing
Is DTG cheaper than screen printing?
For small orders or one-off prints, DTG can be cheaper as it does not require setup costs like screen printing. However, for larger quantities, screen printing is typically more cost-effective.
How long does DTG printing last?
DTG prints can last a long time, especially with proper care (washing inside out, in cold water). The print typically lasts as long as the garment itself if maintained properly.
Is DTG print good quality?
Yes, DTG prints high-quality, detailed, full-color images, making it ideal for complex designs. The quality depends on the machine, ink, and fabric used.
How much for DTG printing?
Costs vary depending on the printer, inks, and materials, but typically range from $1.50 to $5 per garment, depending on design complexity and garment quality.
Which is better, DTF or DTG?
DTF (Direct-to-Film) printing is a method of transferring designs onto a variety of fabrics and surfaces using a film as an intermediary. DTG (Direct-to-Garment) printing is well-suited for printing on cotton fabrics, providing a soft, integrated feel. It’s particularly advantageous for small runs and on-demand printing scenarios.
DTF (Direct-to-Film) printing can be used on multiple fabrics, including cotton, polyester, blends, and non-fabric surfaces like wood and glass. It’s suitable for quickly completing medium to large-scale prints.
Conclusion
In the realm of on-demand manufacturing, DTG printing remains unmatched. If you’re embarking on your entrepreneurial journey, DTG printing offers an easy method to bring your designs to life on fabric, enabling you to launch your brand and make your mark in the market swiftly!
Want to launch your brand quickly? We specialise in a wide range of printed garments and can bring your designs to life quickly!